Can laser equipment cut through any material with absolute precision?
Laser equipment has revolutionized various industries, from manufacturing to medical applications, due to its ability to cut, engrave, and modify materials with high precision.
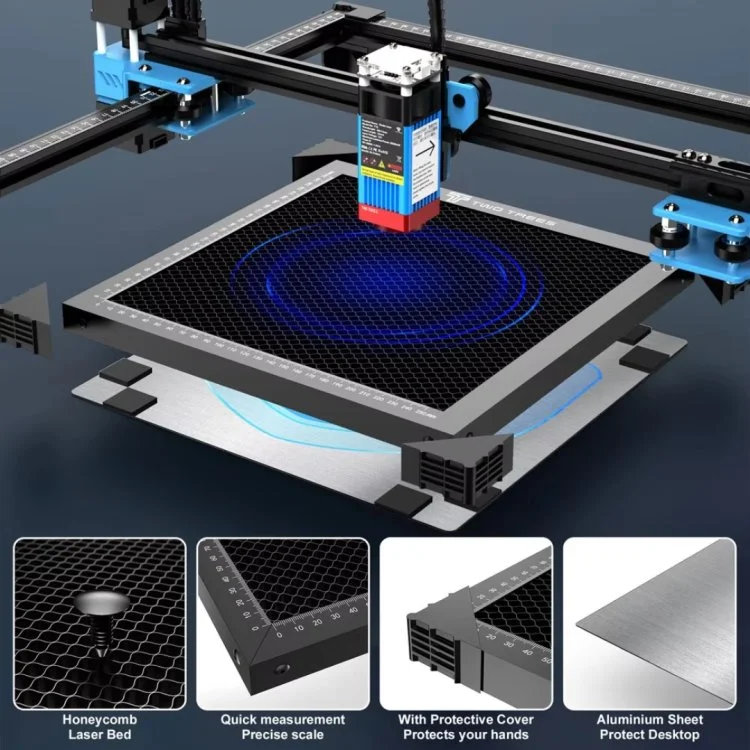
Laser equipment has revolutionized various industries, from manufacturing to medical applications, due to its ability to cut, engrave, and modify materials with high precision. However, the idea that laser equipment can cut through any material with absolute precision is a common misconception. While it is incredibly powerful and versatile, several factors influence its effectiveness, such as material properties, laser type, and operational conditions.
Understanding Laser Equipment and Its Working Principles
Laser equipment functions by generating a concentrated beam of light that delivers energy to a specific point on a material. This energy can melt, burn, or vaporize the material, enabling cutting, engraving, or marking. The key aspects determining laser effectiveness include:
-
Wavelength and Absorption
Different materials absorb laser wavelengths differently. Metals, ceramics, plastics, and composites react uniquely to different laser types, such as CO₂, fiber, and YAG lasers. A material with poor absorption will resist cutting or require higher power. -
Thermal Conductivity
High thermal conductivity materials, like copper and aluminum, dissipate heat quickly, making them more challenging to cut with certain lasers. In contrast, materials like acrylic and wood absorb energy more efficiently, leading to cleaner cuts. -
Reflectivity and Surface Finish
Highly reflective materials, such as polished aluminum or gold, can reflect laser beams, reducing efficiency and potentially damaging the laser system. To counteract this, specialized coatings or pulse-modulated lasers are used. -
Thickness and Density
Thicker and denser materials require higher power levels and slower cutting speeds to achieve precision. While laser equipment can handle a range of thicknesses, extreme cases might necessitate multiple passes or alternative cutting methods.
Types of Laser Equipment and Their Applications
Laser technology is categorized based on the type of laser source used. Each type has its own strengths and is suited for specific applications:
- CO₂ Lasers – Often used for non-metallic materials like wood, acrylic, glass, and leather. They are ideal for engraving and cutting but struggle with reflective metals.
- Fiber Lasers – Highly efficient for cutting metals such as steel, aluminum, and brass. These lasers have a concentrated beam, allowing for high precision.
- Diode Lasers – Common in small-scale applications like engraving and marking. They are not as powerful as fiber or CO₂ lasers.
- Nd:YAG and Nd:YVO4 Lasers – Typically used in industrial and medical fields, especially for marking and drilling applications.
Challenges Faced by Laser Equipment in Cutting Certain Materials
While laser equipment is highly advanced, certain materials present significant challenges:
- Transparent Materials: Glass and clear plastics allow light to pass through, making it difficult for certain laser types to interact effectively. Specialized coatings or specific wavelengths help address this issue.
- Highly Reflective Metals: As mentioned earlier, metals like copper, gold, and aluminum can reflect the beam, leading to inefficiencies and potential equipment damage. Fiber lasers are usually preferred for such materials.
- Heat-Sensitive Materials: Some plastics and composites may burn or emit toxic fumes when exposed to laser cutting, requiring controlled settings and proper ventilation.
- Ceramics and Stones: These materials are hard and brittle, making them difficult to cut cleanly. CO₂ lasers with specialized techniques can be used, but precision may be affected.
Factors Affecting Precision in Laser Cutting
Achieving absolute precision with laser equipment depends on multiple factors:
- Beam Focus and Alignment – The focus of the laser beam determines the accuracy of the cut. A well-focused beam ensures minimal material distortion and clean edges.
- Cutting Speed and Power Settings – Adjusting speed and power settings is crucial for different materials. Higher power may cause burns, while lower power may lead to incomplete cuts.
- Assist Gases – Oxygen, nitrogen, and air assist in removing melted material and improving cut quality. The choice of gas depends on the material being processed.
- Machine Calibration and Maintenance – Regular calibration ensures consistent performance. Misalignment or lens contamination can impact precision.
Common Myths About Laser Equipment
1. "Laser Equipment Can Cut Through Any Material with Ease"
While laser equipment is powerful, not all materials can be cut efficiently. Factors such as reflectivity, heat resistance, and absorption properties affect the outcome.
2. "All Laser Equipment Delivers the Same Results"
Different types of lasers have different applications. A CO₂ laser is excellent for cutting acrylic but ineffective for metals, while a fiber laser excels at metal cutting.
3. "Laser Cutting is Always a Perfectly Clean Process"
While laser cutting minimizes waste, some materials may produce burn marks, debris, or require post-processing. Proper settings and ventilation systems help mitigate these issues.
Safety Considerations When Using Laser Equipment
Due to the high-intensity beams and heat generation, laser equipment must be used with safety measures in place:
- Protective Eyewear – Direct exposure to laser beams can cause eye damage. Specialized goggles based on the laser’s wavelength should be worn.
- Ventilation Systems – Cutting certain materials produces fumes and particles that can be hazardous. Proper ventilation or fume extraction systems are necessary.
- Fire Hazards – Some materials, like wood and plastics, are flammable. Monitoring the process and having fire suppression measures in place is crucial.
- Machine Enclosures and Safety Interlocks – Many industrial laser machines have protective enclosures to prevent accidental exposure to the beam.
Future of Laser Equipment and Technological Advancements
Laser technology continues to evolve, with new advancements improving efficiency, speed, and precision. Some emerging trends include:
- Ultrafast Lasers – Shorter pulse durations allow for even finer and cleaner cuts, reducing heat-affected zones.
- Hybrid Laser Systems – Combining different laser types enhances versatility and expands material compatibility.
- AI and Automation – Machine learning algorithms optimize cutting paths, reduce waste, and improve precision.
- Green Lasers – New wavelengths tailored for challenging materials, such as highly reflective metals, are in development.
Conclusion
Laser equipment is an indispensable tool across industries, but it is not a universal solution for every material. While it delivers exceptional precision under optimal conditions, factors such as material properties, laser type, and operational settings influence the outcome. Understanding these intricacies ensures better utilization of laser technology while avoiding unrealistic expectations.
So, can laser equipment cut through any material with absolute precision? The answer is no—its effectiveness depends on multiple variables. However, with proper selection, calibration, and expertise, laser equipment remains one of the most advanced and versatile tools in modern manufacturing and fabrication.
What's Your Reaction?






