Challenges and Solutions in Welding Robot Integration
Welding robots have transformed the manufacturing sector by enhancing productivity, precision, and consistency in welding operations. However, integrating these advanced systems into existing workflows presents multiple challenges. Factors such as technical complexity, high initial costs, and the need for skilled personnel can create obstacles in seamless adoption.
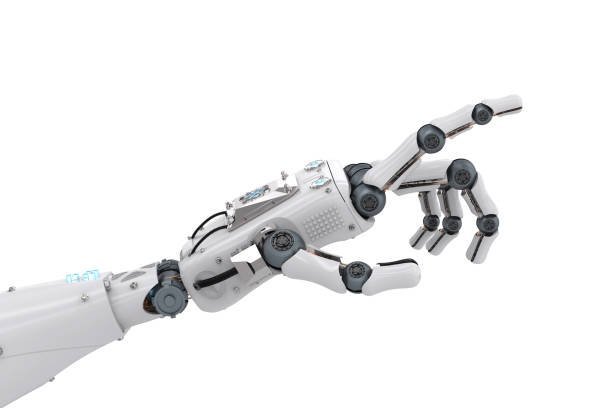
Introduction
Welding robots have transformed the manufacturing sector by enhancing productivity, precision, and consistency in welding operations. However, integrating these advanced systems into existing workflows presents multiple challenges. Factors such as technical complexity, high initial costs, and the need for skilled personnel can create obstacles in seamless adoption. Despite these hurdles, strategic solutions can optimize welding robot integration, ensuring businesses achieve maximum efficiency and quality.
Challenges in Welding Robot Implementation
One of the primary challenges in adopting welding robots is the high initial investment. The cost of acquiring robotic welding systems, along with additional expenses for installation and training, can be a significant barrier for many industries. Furthermore, integrating these systems with existing production lines requires careful planning and customization to ensure compatibility with current processes. This complexity often leads to extended downtime and higher operational costs during the transition phase.
Another major concern is the requirement for skilled personnel to operate and maintain welding robots. While automation reduces the dependence on manual labor, it necessitates a workforce with specialized knowledge in programming, troubleshooting, and system optimization. Many industries face difficulties in sourcing or upskilling employees to handle these advanced robotic systems effectively. Additionally, ensuring consistent weld quality across various materials and joint configurations requires precise calibration and real-time monitoring, adding to the complexity of integration.
Effective Solutions for Welding Robot Integration
To overcome these challenges, industries can implement strategic solutions such as phased adoption and workforce training programs. A gradual transition to automated welding allows businesses to optimize processes without disrupting production. Conducting pilot projects and investing in modular robotic systems can help in testing efficiency before full-scale deployment. Additionally, collaboration with experts in automation technology can streamline the integration process, ensuring compatibility with existing infrastructure.
Enhancing workforce capabilities through specialized training programs is crucial for maximizing the benefits of welding robots. Providing hands-on experience in programming, operation, and maintenance enables employees to handle robotic systems efficiently. Furthermore, leveraging advanced technologies such as artificial intelligence (AI) and machine learning (ML) can improve welding accuracy through real-time monitoring and adaptive adjustments. Implementing predictive maintenance strategies also ensures long-term reliability, minimizing unexpected downtimes and repair costs.
Conclusion
While welding robots offer significant advantages in precision and efficiency, their integration into manufacturing processes comes with challenges. High costs, technical complexities, and skill gaps can hinder smooth adoption. However, by implementing phased deployment, investing in workforce training, and leveraging advanced technologies, industries can successfully integrate welding robots into their production lines. With proper planning and strategic execution, welding automation can revolutionize industrial operations, leading to improved productivity and long-term profitability.
What's Your Reaction?






