Exploring the Diverse World of Instrumentation Tube Fittings
Discover the intricacies of instrumentation tube fittings, from compression fittings to flare fittings and beyond. Explore their applications, materials, and advantages in various industries for precise and reliable fluid system connections.
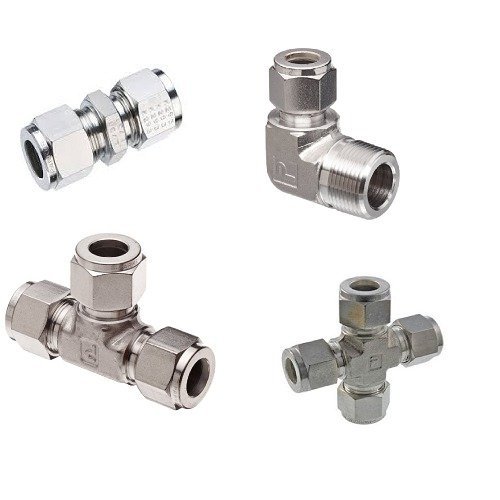
Instrumentation tube fittings are the unsung heroes of fluid control systems, providing the crucial link between tubing, valves, gauges, and instruments. With a plethora of options available, each tailored to specific applications, exploring the diverse world of instrumentation tube fittings unveils a landscape of innovation and precision engineering. In this blog, we’ll delve into the various types of instrumentation tube fittings, their unique features, and the industries they serve.
-
Compression Fittings:
- Compression fittings employ a ferrule and compression nut to create a secure and leak-tight connection between tubing and fittings.
- They are renowned for their ease of installation, reliability, and ability to withstand high pressures and vibrations.
- Commonly used in industries such as oil and gas, chemical processing, and instrumentation systems requiring precise fluid control.
-
Tube Fittings:
- Tube fittings, also known as tube connectors or tube adapters, provide versatile solutions for connecting tubing to valves, manifolds, and instruments.
- Available in various configurations including straight connectors, elbows, tees, and crosses, allowing for flexibility in piping layouts.
- Ideal for applications in industries such as water treatment, pharmaceuticals, and semiconductor manufacturing, where cleanliness and precision are paramount.
-
Threaded Fittings:
- Threaded fittings feature male or female threads for convenient screwing onto other components such as valves and instruments.
- They provide a secure and reliable connection, especially in applications where frequent disassembly and reassembly are required.
- Widely used in process industries, HVAC systems, and plumbing installations for their ease of installation and versatility.
-
Flare Fittings:
- Flare fittings utilize a cone-shaped flare on the tubing end, which mates with a matching flare seat on the fitting body to create a leak-tight seal.
- Known for their resistance to vibration and high pressures, making them suitable for demanding applications such as hydraulic systems and refrigeration.
- Commonly found in automotive, aerospace, and marine industries where reliability and performance are critical.
-
Push-to-Connect Fittings:
- Push-to-connect fittings, also known as quick-connect fittings, offer rapid and tool-free installation by simply pushing the tubing into the fitting.
- They feature a gripping mechanism that securely holds the tubing in place, providing a reliable and leak-tight connection.
- Ideal for applications requiring fast assembly and disassembly, such as pneumatic systems, automotive manufacturing, and robotics.
Conclusion:
Stainless Steel Instrumentation Tube Fitting encompass a diverse range of solutions tailored to meet the demanding requirements of modern industrial applications. From compression fittings providing robustness in high-pressure environments to push-to-connect fittings offering rapid assembly in dynamic systems, the world of instrumentation tube fittings continues to evolve, driven by innovation and technological advancements. By understanding the unique features and capabilities of each type of fitting, engineers and industry professionals can select the most suitable solution to ensure optimal performance and reliability in their fluid control systems.
What's Your Reaction?






