Polypropylene in the Automotive Industry: The Game-Changer You Didn't See Coming
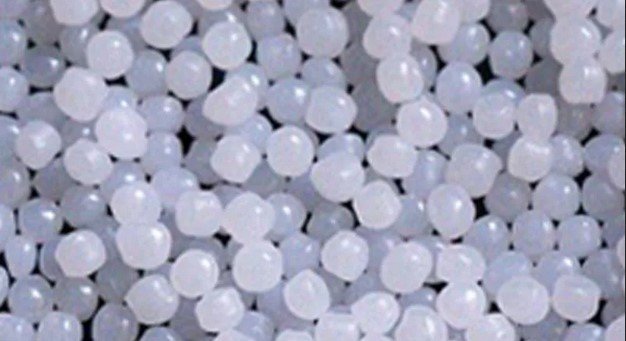
The automotive industry is in constant evolution, with manufacturers seeking ways to improve vehicle efficiency, safety, and sustainability. One material that has emerged as a true game-changer in this space is polypropylene (PP). Once considered a basic plastic, polypropylene is now revolutionizing car manufacturing due to its unique blend of lightweight properties, durability, cost-effectiveness, and environmental benefits.
From interior components to under-the-hood applications, Polypropylene Material is helping automakers meet modern demands for fuel efficiency, electrification, and recyclability. But how exactly is this versatile polymer reshaping the automotive landscape? Let’s explore why polypropylene is the game-changer you didn’t see coming.
What Is Polypropylene?
Polypropylene (PP) is a thermoplastic polymer widely used across various industries due to its high impact resistance, chemical stability, and lightweight nature. It is a semi-crystalline polymer that offers excellent mechanical properties and can be easily molded into different shapes.
One of the key advantages of polypropylene is that it is recyclable and can be reprocessed multiple times, making it a preferred choice for sustainable automotive manufacturing.
Key Properties of Polypropylene
- Lightweight – 30-40% lighter than metals
- Durable – High resistance to impact and fatigue
- Heat Resistant – Can withstand high engine temperatures
- Chemical Resistant – Resistant to corrosion and automotive fluids
- Cost-Effective – Affordable compared to metals and engineering plastics
- Recyclable – Reduces waste and environmental impact
The Rise of Polypropylene in the Automotive Industry
The increasing use of polypropylene in vehicles is largely driven by two major industry trends:
The Push for Lightweight Vehicles
- Stricter fuel efficiency and emissions regulations require automakers to produce lighter cars.
- Polypropylene reduces overall vehicle weight, improving fuel economy and lowering carbon emissions.
- In electric vehicles (EVs), lighter materials extend battery range.
Sustainability & Recycling Demands
- The automotive industry is under pressure to adopt eco-friendly materials.
- Polypropylene can be recycled and reused, supporting circular economy models.
- Recycled PP is now used in dashboards, door panels, and bumpers.
With these trends in mind, let’s take a deeper look at how polypropylene is used in various automotive applications.
Polypropylene’s Role in Different Car Components
- Interior Applications
Polypropylene is a dominant material in car interiors due to its ability to be easily molded, textured, and colored.
Key Uses in Interiors:
- Dashboards & Instrument Panels – Provides a lightweight and impact-resistant structure.
- Door Panels – Offers a cost-effective alternative to heavier materials.
- Seating Components – Used in seat backs and trims for durability.
- Carpets & Floor Mats – Made from polypropylene fibers for stain resistance.
With automakers focusing on aesthetics, safety, and weight reduction, polypropylene is the go-to material for modern car interiors.
- Exterior Applications
PP’s toughness and ability to withstand harsh conditions make it ideal for exterior components.
Key Uses in Exteriors:
- Bumpers – PP’s impact resistance makes it the best material for absorbing shocks.
- Grilles & Fenders – Lightweight yet durable, helping reduce overall vehicle weight.
- Headlight Housings – Resistant to heat and UV exposure.
These applications showcase how polypropylene contributes to both safety and aerodynamics in modern vehicle designs.
- Under-the-Hood Components
Polypropylene is increasingly used in engine components and under-the-hood applications due to its heat and chemical resistance.
Key Uses Under the Hood:
- Battery Casings – Used in both traditional and electric vehicles (EVs).
- Air Intake Manifolds – Lightweight and durable alternative to metal.
- Coolant & Washer Fluid Reservoirs – Resistant to automotive fluids.
With EV production on the rise, polypropylene is playing a critical role in battery systems and thermal management components.
The Future of Polypropylene in Cars
The demand for electric vehicles, autonomous cars, and sustainable manufacturing is driving new innovations in polypropylene use. Some of the exciting advancements include:
- Bio-Based Polypropylene – Researchers are developing plant-based PP to further reduce carbon footprints.
- Advanced Composites – PP blended with fiberglass or carbon fiber to enhance strength.
- 3D Printing with PP – Enabling customized automotive parts with faster production times.
- Self-Healing PP Materials – Future developments may allow PP to repair itself after minor damages.
These breakthroughs will further solidify polypropylene’s role in shaping the next generation of automobiles.
Conclusion: A Game-Changer for the Automotive Industry
Polypropylene is no longer just another plastic – it is a key enabler of modern automotive innovation. With its lightweight, durability, cost-efficiency, and recyclability, it is helping automakers meet the evolving demands of fuel efficiency, EV production, and sustainability.
As the industry moves towards a greener, more efficient future, expect polypropylene to play an even bigger role in the cars of tomorrow. Whether it's enhancing safety, reducing weight, or driving sustainability, this material is truly a game-changer you didn’t see coming.
Plastic4trade is a globally B2B plastic trade solution and source related of polymer news and Polymer price that it promises will permanently transform the way of plastics and polymers are traded. The Plastic4trade Android app, iOS App and website make polymer trading simple and efficient. Plastic industries people may use this trading application to post their queries for free. It is a plastic trade solution tool that allows buyers and sellers to publish their needs, interact, talk, and make important trade calls using the app.
What's Your Reaction?






