Top Maintenance Tips for Heavy Machinery and Equipment
Discover essential maintenance tips to keep your heavy machinery and equipment running smoothly, reducing downtime and boosting efficiency.
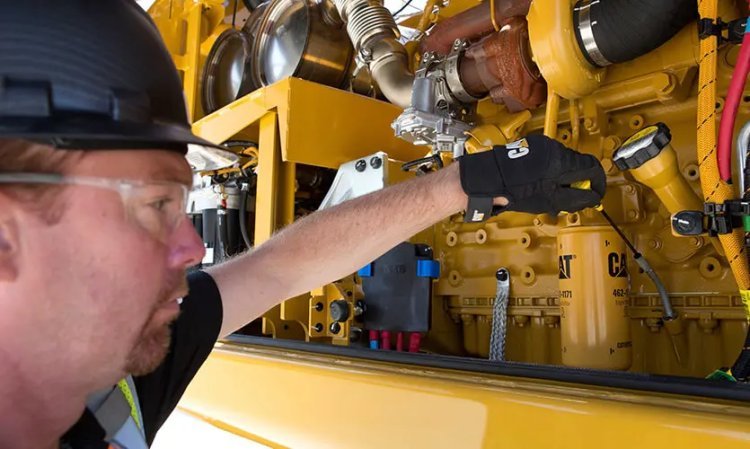
Proper maintenance of heavy machinery and industrial equipment is essential for efficient operations and longevity. For companies in Australia, investing in protective measures and regular checkups ensures equipment remains reliable. Adding protection options, like the Graphene Coating offers, can help safeguard machinery in demanding environments. Following a structured maintenance plan keeps machines running smoothly and helps avoid costly repairs or downtime.
Given the high cost of such equipment, companies are increasingly investing in protective solutions and structured maintenance routines to extend the lifespan of their assets. Whether it’s safeguarding against corrosion, wear, or environmental damage, proper care can significantly impact the performance and reliability of these machines. Selecting the right protective methods and maintenance strategies can be a game-changer for productivity and long-term equipment value.
1. Understanding Equipment-Specific Needs
Each type of machinery has unique maintenance requirements. Cater to these needs for better performance.
Manufacturer Guidelines: Refer to the manufacturer’s manual for recommended maintenance intervals and methods.
Critical Components: Some parts, such as engines or hydraulics, need more frequent attention.
Operating Environment: Machines in harsher conditions may require additional care, such as special coatings or increased lubrication.
Knowing what each machine requires helps tailor your maintenance approach, making it more effective.
2. Establishing a Preventive Maintenance Schedule
Preventive maintenance minimises unexpected breakdowns by addressing minor issues before they escalate.
Daily Checks: Basic daily inspections can help catch small problems early.
Monthly Inspections: More in-depth monthly checks might include lubrication and filter changes.
Annual Maintenance: A comprehensive inspection annually ensures your equipment stays in top condition.
Preventive maintenance saves time and money by reducing the risk of unplanned repairs.
3. Keeping Machinery Clean
Dirt, dust, and debris can damage equipment over time. Regular cleaning prevents wear and tear.
Regular Washdowns: Clean machinery regularly to remove dust, mud, and other residues.
Compressed Air: Use compressed air to blow dust from hard-to-reach areas without disassembling equipment.
Rust Prevention: In humid areas, rust can quickly form on metal parts. Clean and dry equipment properly to prevent this.
A clean machine not only performs better but also lasts longer.
4. Lubrication for Longevity
Proper lubrication reduces friction, which in turn minimises heat and wear on parts.
Oil Sampling: Regularly testing oil samples helps spot contaminants or early signs of wear.
Right Lubricant Selection: Follow manufacturer recommendations for oils and greases to ensure compatibility.
Application Frequency: Over-lubrication can be just as damaging as under-lubrication, so apply only as needed.
Lubricating moving parts keeps machinery operating efficiently, with less wear and tear.
5. Upgrading Coatings for Enhanced Durability
New coating technologies provide durable protection against corrosion, chemicals, and extreme conditions.
Eco-Friendly Coatings: Low-VOC and environmentally safe coatings reduce environmental impact.
Graphene Coatings: This emerging technology offers a high level of durability and chemical resistance.
Impact of Ceramic Coatings: Ceramic coatings provide excellent protection for high-wear parts, helping reduce maintenance.
Protective coatings are a great investment for extending the life of your machinery in challenging environments.
6. Prioritising Electrical System Checks
Modern heavy machinery relies on electrical systems, which need regular checks to stay reliable.
Battery Inspections: Batteries degrade over time; regular testing ensures they stay operational.
Wire Checks: Vibrations can loosen wiring, which could lead to malfunctions.
Fuse Replacements: Inspect fuses and replace those that show signs of wear.
Monitoring electrical components helps avoid sudden machinery stoppages and ensures smooth operations.
7. Operator Training and Skill Development
Operators play a key role in maintaining machinery. Proper training can prevent accidental damage.
Basic Troubleshooting: Teach operators how to handle minor issues on the spot.
Daily Performance Logs: Keeping logs helps operators notice and report unusual performance quickly.
Safety Awareness: Training on safety protocols helps prevent accidents that might damage equipment.
Well-trained operators contribute significantly to equipment lifespan by following proper handling techniques.
8. Monitoring and Logging Performance Metrics
Monitoring key performance metrics offers insights into machinery health and identifies potential issues.
Fuel Efficiency Tracking: Declines in fuel efficiency may indicate a need for maintenance.
Output Rates: Tracking output helps spot any deviations from normal productivity levels.
Maintenance Logs: Regularly updated logs provide a history of repairs, helping inform future maintenance.
Tracking performance data helps make informed decisions about repairs and replacements.
9. Adjusting for Seasonal Conditions
Different seasons require adjustments in machinery care. Planning for seasonal changes can help maintain machinery durability.
Hot Weather Precautions: Use cooling solutions and shade to prevent overheating in summer.
Winter Protection: Switch to winter-grade lubricants and check heating components in colder months.
Humidity Control: Equipment in humid areas can benefit from additional protection like the 9H Ceramic Coating option, which offers resistance to rust and corrosion.
Seasonal adjustments reduce the strain on machinery, helping extend its operational life.
10. Understanding the Benefits of Regular Inspections
Regular inspections allow you to catch problems before they require costly repairs.
Wear and Tear Identification: Inspections help catch worn parts before they fail.
Safety Compliance: Regular checks ensure machinery remains compliant with safety standards.
Timely Repairs: Spotting issues early allows you to address them without disrupting operations.
Routine inspections are a vital part of any successful maintenance plan, promoting both safety and reliability.
11. Making Use of Technology and Digital Tools
Advanced technology simplifies maintenance processes and provides actionable insights.
Sensors and IoT: Sensors monitor real-time data, alerting operators to any issues immediately.
Maintenance Software: Digital tools help plan and track maintenance schedules efficiently.
Predictive Analytics: Using data analytics to predict potential failures helps optimise maintenance.
Technology-based tools can streamline maintenance, improving both accuracy and efficiency.
Conclusion
Maintaining heavy machinery requires a strategic approach, with attention to everything from daily inspections to seasonal adjustments. Keeping a routine and focusing on the needs of each machine ensures smooth operation and minimises costly breakdowns. By following these tips, machinery owners can ensure their investments remain productive and efficient for years to come.
Additionally, investing in protective measures, such as 9H Ceramic Coating, offers an added layer of defence against harsh environmental conditions, contributing to the long-term durability of your equipment. Taking a proactive approach ensures smoother operations, reduces downtime, and ultimately boosts overall operational efficiency.
What's Your Reaction?






